Production
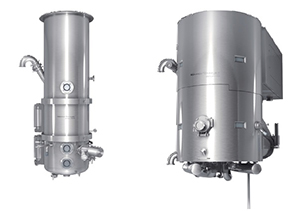
Romaco Innojet VENTILUS®
Production Scale Series
The production scale systems in the Romaco Innojet VENTILUS® series are designed for batch sizes from 40 to 1,600 litres. The technology is utilised in the pharmaceutical, food and chemical industries.
Different LE (Light Edition) and Premium Versions Provide Application Flexibility
- VENTILUS® LE-D: for drying processes (optionally in combination with high-shear mixer)
- VENTILUS® LE-G: for granulation processes
- VENTILUS® LE-C: for granulation and coating processes
- VENTILUS® Premium: «all-in-one» system with slide-out nozzle support, allowing spray nozzle changes without interrupting the process
- Modular upgrade from a VENTILUS® LE-D dryer to a VENTILUS® LE-G granulator is a simple matter
- Larger batch volumes or modifications on request
Highlights
- WIP – washing in place: product-contacted parts inside the system are cleaned automatically
- Strictly hygienic design of the interior speeds up cleaning
- Special design of the ORBITER booster and the restriction to a single ROTOJET spray nozzle enable significantly shorter cleaning time after each batch
- Filters washed in place as part of pre-cleaning after the process
- Filters also available in a stainless steel CIP (cleaning in place) version
- Inner cores and seals of the complete process filter are cleaned during washing
- Small number of inflatable seals
GMP Granulation Line Concept
VENTILUS® systems can also be used as part of a multi-purpose wet granulation line in combination with a high-shear mixer. Owing to their application flexibility, they are ideal for contract manufacturing. The closed material transfer system has a built-in conical mill for wet and dry milling.
- Horizontal product flow with a compact design and small footprint in the cleanroom
- Discharge into different container sizes with a conical mill that is suitable for both wet and dry milling processes
- Ergonomic, integral cleaning of all complementary equipment
- Ex concept with interconnected process containers for fast and reliable transfer of intermediates
Technical Data
Technical data | V 100 | V 200 | V 300 | V 400 | V 600 | V 800 | V1000 | V 1200 | V 1600 |
Max. batch size (kg, at 1g/cm³) Premium and LE-C | 100 | 200 | 300 | 400 | 600 | 800 | 1,000 | 1,200 | 1,600 |
Max. batch size (kg, at 0.5g/cm³) LE-D and LE-G | 50 | 100 | 150 | 200 | 300 | 400 | 500 | 600 | 800 |
Min. batch size (kg, at 1g/cm³) Premium and LE-C | 40 | 80 | 120 | 160 | 240 | 320 | 400 | 480 | 640 |
Min. batch size (kg, at 0.5g/cm³) LE-D and LE-G | 20 | 40 | 60 | 80 | 120 | 160 | 200 | 240 | 320 |
Product container inside ø = booster ø (mm) | 650 | 800 | 950 | 1,100 | 1,200 | 1,350 | 1,500 | 1,600 | 1,600 |
Air quantity (m³/h) Premium and LE-C | 2,200 | 3,200 | 4,200 | 5,500 | 6,500 | 8,500 | 10,000 | 12,000 | 15,000 |
Air quantity (m³/h) LE-D and LE-G | 1,200 | 1,800 | 2,300 | 3,000 | 4,000 | 5,000 | 6,000 | 8,000 | 9,000 |
Spray air quantity (Nm³/h at 3.0 bar spray pressure) | 150 | 250 | 250 | 400 | 400 | 500 | 500 | 600 | 600 |
Steam pressure (barg/bara) | 3.5 (4.5) | ||||||||
Cooling water for dehumidification (glycol-free) (forward/return) (°C) | 6/12 | ||||||||
Power consumption (KW) | 32 | 44 | 65 | 70 | 85 | 100 | 115 | 135 | 170 |
Particle size min. (μm) | 10 | ||||||||
Particle size max. (mm) | 2 | ||||||||
Materials (product-contacted) | Stainless steel AISI 316l Borosilicate glass Filter media, plastic and seals FDA certified | ||||||||
Pressure shock resistance (bar) | 10 |